Filtration, purification and separation: the essential trifecta of sample preparation
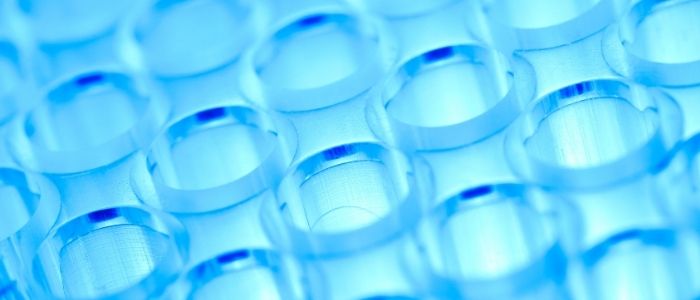
It may not be the most glamourous of processes, but filtration, purification and separation are essential aspects of sample preparation, vital to almost all researchers’ day-to-day work.
One company, Pall Corporation (NY, USA), is attempting to improve the lives of these researchers, creating 24-well filter plates that will save the researchers time, reduce the opportunities for error and minimize plastic waste. To introduce a new range of 24-well filter plates with high-performance membranes, viable for numerous applications, Pall’s Global Product Manager Lori Euler, speaks to BioTechniques about the challenges they overcame and the benefits they afford – without the need to alter your workflows.
Read the full-length interview, featured in condensed form in our latest eBook: Lab essentials: optimizing sample preparation and product purification, below.
Pall specializes in techniques for sample preparation, mainly purification, filtration and separation. What are some of the key applications of these three techniques?
There is a broad range of applications for these techniques but specifically, our molecular portfolio and our plate portfolio are often used in sample preparation for downstream analysis, from protein binding studies and sequencing to analytical QC assays. Essentially, whenever a study requires work to be done in a plate format, a filter plate can be introduced to the workflow to help streamline the process. This means that updating these foundational processes can have a huge impact on the daily work of many researchers.
What are some of the current challenges associated with working in plate formats?
As researchers begin to work with larger sample volumes, scaling up their workflows to deliver higher throughput processes they often find that there are no solutions for them. A lot of these researchers work with automated workflows that involve plate-based steps. Without filter plates that can handle larger sample volumes, these researchers would need to leave plate formats behind in order to scale up, which can be very challenging. The introduction of our new 24-well filter plate portfolio strives to fill this huge gap in the industry across multiple filtration types including ultrafiltration, microfiltration, and particle filtration. This new range allows them to stay in the same, automation-friendly format, giving them the ability to optimize their workflow.
You’ve just mentioned your new 24-well filter plate range, can you introduce us to some of the key products in that range?
First, we have our Omega™ membrane, which is our ultrafiltration membrane with a molecular weight cut-off ranging from 1K to 100K. This gives researchers working with multiple different proteins a selection of molecular weight cut-offs to choose from. This Omega membrane is used by Pall in many other devices allowing seamless integration of these 24-well filter plates into existing workflows. There is no need for new membrane validations, there is no need to add time-consuming or wasteful steps. Those who may be using a 96-well plate, trying to scale up and using spin devices or Tangential flow filtration, can now keep the same membrane throughout the entire range of volumes they want to work with.
Second, is our Supor® membrane, which has very broad applications, for example, sterile filtration or pre-filtration. Often researchers will have particulates in a sample that they need to remove to prevent contamination or interference with downstream results and analysis. A wide range of pore sizes in the Supor membrane – from 0.1 um to 5 um – allows researchers to perform everything from mycoplasma reduction to bead-based assays and resin screening in larger volumes. Again, the Supor membrane is used throughout our devices so we can scale with our customers.
The last thing we added was something a little bit unique. It’s a plate with a very large membrane pore size that is great for researchers working with plants. This membrane filters what we call gross particulates, things like plant material.
So, integrating these plates into existing workflows is going to be very simple for researchers?
Absolutely. Researchers can choose to centrifuge these plates, they can use a vacuum manifold, they can use positive pressure. Our goal was seamless integration into existing workflows. All of our plates are ANSI standard so they work with all liquid handling and plate-based equipment and systems a researcher may have.
Which industry do you imagine these new membranes and new plates are going to have the biggest impact on?
I believe that the biopharma industry will see the biggest impact, mainly because they’re already using higher throughput techniques like compound screening. These 24-well filter plates will allow them to bridge that gap between high throughput process development and scale up. But the key with the new plates is the volume that the customer needs to filter. If they are using between 2–7 mL, this is the solution for them. Therefore, these new filter plates will have an impact in Biopharma as well as many other industries.
Have you seen any impact or excitement from researchers who have started using these plates?
The biggest challenge at launch was communicating awareness that this brand-new plate format and portfolio is available. 24-well filter plates for all these applications has never existed, so customers are not actively searching for it. Once customers became aware of the availability and wide variety of options, many got quite excited. After testing, the feedback around performance and workflow improvements has been very positive. Even during our beta testing, we kept getting asked “Are they ready yet? Are they ready yet?”. Customer response has been great, the struggle is informing the world these new game-changing filter plates are available to them.
Do these plates have an economic or environmental impact?
Yes and Yes. Because we have so many membranes, there are multiple steps that can be combined. For instance, you can do a prefiltration step through one plate, and then concentration of a protein through another plate – all automated if you wish. Currently, you would need to go through individual syringe filters and that can involve 24 individual manual steps for each sample and each step would consume a filter, the barrel, the tube and more! In this example the 24-well filter plates can provide a huge reduction in plastic waste, we have measured up to 7X reduction in plastic waste by weight.
The other key is that every time the sample passes through a membrane you risk sample mishandling or losing sample on the membrane. Now the sample can all be loaded into one 24-well plate and you minimize the chance for those errors to occur.
What do you think are some of the next challenges to be addressed in sterile filtration, purification and separation?
Researchers’ needs are changing so rapidly at the moment it is difficult to be sure. I think making membrane selection simpler is an interesting area to look at. Being able to streamline workflows further by combining or reducing steps would also be very helpful to so many people. We have done this in our clarification and sterile filtration plate which has three different membranes and can sterile filter proteins from a cell culture in a single step.
Is there anything that people looking to acquire these plates should look out for or be aware of beforehand?
I think the biggest thing is to understand is that not all membranes are going to process the same way. If a customer has always used our Supor membrane, and now they have some ultra-filtration needs, it is important to take the time to understand the differences in processing. These differences include things like the time to process, starting conditions and the speed of your centrifuge.
The biggest challenge with the 24-well plate is for any customer who wants to use a centrifuge. These are tall plates to accommodate 7mL, we have designed them to fit into most centrifuges. But it’s always a good idea just to check the specifications of your rotor to make sure that it can swing freely with the plates inside. This is easy to check with the centrifugation rotor in your lab and we provide all these specifications for the plates as well.
Additionally, watch for and understand claims of any filter plate used. Not all filter plates are equal and we’ve specifically designed manufacturing processing and testing to ensure our new 24-well filter plates have strong and supported claims, such as sterile effluent and gamma irradiation.
If you could design the filter plate of your dreams, the 24-well filter plate that you think would solve all researchers’ problems, what would you design?
Wow, that is a tough question! I honestly think we came up with a great design for this plate but if we could find other ways to combine steps, maybe a prefiltration before ultrafiltration, I think that might be really interesting to explore. To mix and match, combining membranes into one plate.
To find out more about Pall’s 24-well plate range visit: www.pall.com/en/laboratory/filter-plates/24-well.html